[ad_1]
The Pantheon in Rome, inbuilt AD 126 by the Emperor Hadrian, and 1 Wall Road, a Decrease Manhattan skyscraper not too long ago transformed into luxurious condos, won’t seem comparable at first look.
The grand concrete dome boasts an inside coffered to scale back weight; sunken rectangular patterns pressed into the wall lower its weight, permitting it to face with out helps. The highest flooring of 1 Wall Road, in the meantime, comprise air-filled plastic shapes to make the concrete flooring much less cumbersome.
[Photo: courtesy Cobiax]
Each showcase completely different variations of historical concrete development methods that take away among the materials utilized in a ground or span to make the construction lighter, eliminating the necessity for extra helps and reinforcement. Some engineers imagine they will additionally use this concept to unravel a very knotty trendy architectural drawback: reducing carbon emissions.
On the newly redeveloped 1 Wall Road, first inbuilt 1929, a method referred to as voided concrete makes use of empty areas inside concrete slab flooring. Earlier than the slab units, staff insert air-filled cavities—ancients used empty terracotta blocks, right this moment’s builders use two-by-two-feet plastic spheres—that create the namesake voids because the flooring harden round them.
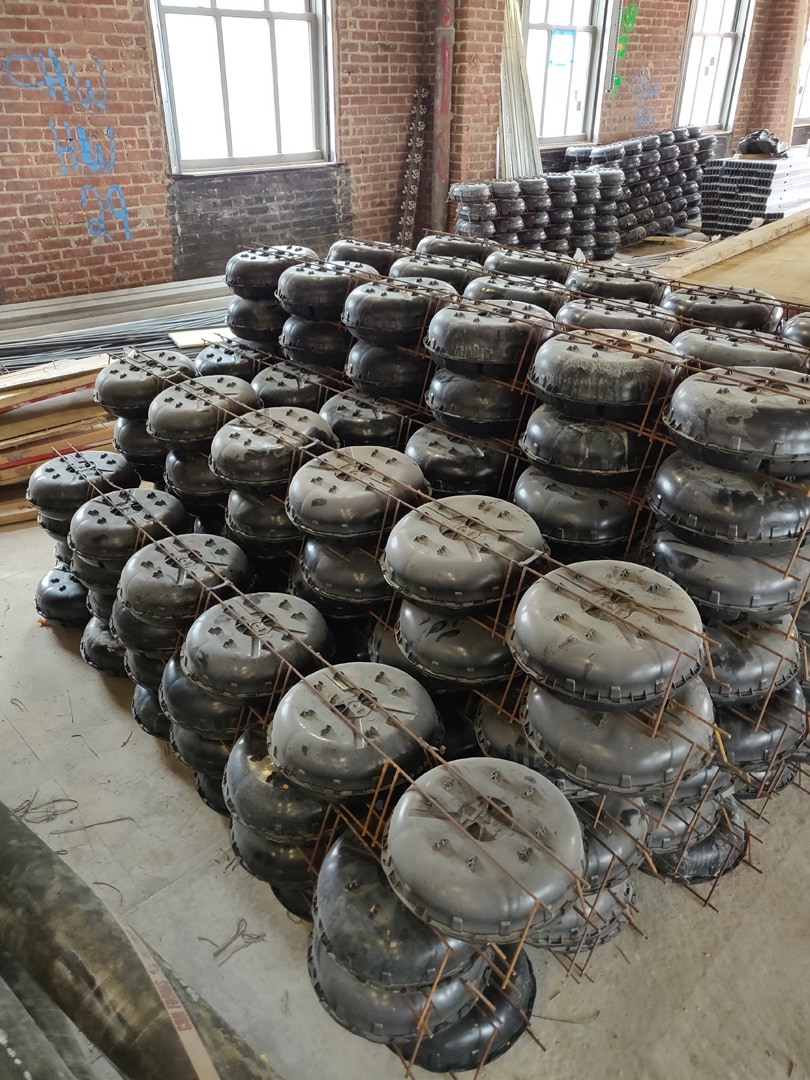
[Photo: courtesy Cobiax]
Giant concrete flooring discovered inside high-rises comprise a grid of metal beams, or rebar, for assist, and weigh a major quantity. Utilizing voids to scale back the quantity of concrete decreases the general weight and want for columns and helps, all with out eradicating any inside assist or structural power.
Mark Plechaty, a principal at DeSimone Consulting Engineers in New York Metropolis, which labored on the 1 Wall Road venture, has used the method on each conversions and ground-up initiatives for the final six years. His agency has found voided concrete slabs in New York Metropolis buildings constructed way back to the Twenties. He says these cut back the burden of a ground by a 3rd or extra, requiring much less concrete and reducing emissions. On high of that, he argues that it may possibly additionally assist make office-to-residential conversion initiatives extra inexpensive, and due to this fact extra possible: Including additional flooring for extra flats turns into inexpensive, since they are often lighter and require much less assist and reinforcement.
“I wouldn’t say that this all of the sudden makes the entire thing viable,” says Plechaty. “But it surely helps quite a bit. It’s a giant issue.”
At 1 Wall Road, these voided concrete slabs have been used so as to add extra flooring. The added slabs ended up weighing much less, that means the decrease flooring and basis required fewer expensive reinforcements to assist the burden. Filling the ground with what have been successfully air bubbles made it less expensive so as to add six flooring to the highest of the constructing, rising the rentable sq. ft. Engineers have estimated that every pound of plastic balls used to create voids eliminates 100 pounds of concrete.
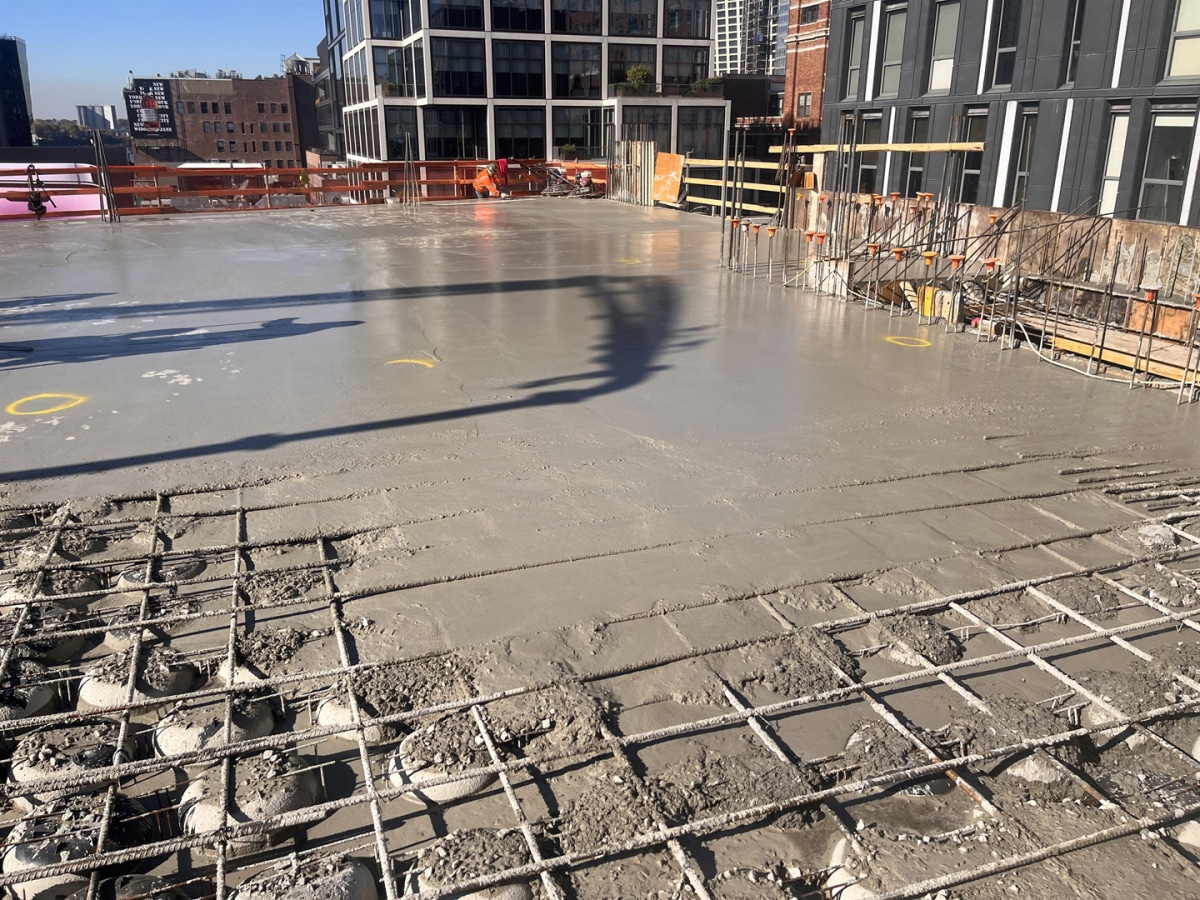
[Photo: courtesy Cobiax]
Plechaty additionally factors to a examine DeSimone did for developer HFZ, which planned to construct a skyscraper on twenty ninth Road and fifth Avenue in New York Metropolis utilizing this system. (Finally, the venture was scrapped.) The voided concrete flooring proposed would have been considerably thinner, with 20-inch deep helps as a substitute of 36-inches. Multiply that 16-inch distinction by 54 flooring, and that shaves 72 ft off the constructing, which meant $8 million much less in glass home windows alone. Constructing operations additionally would have benefitted from the minimize off the highest, with much less house to warmth and funky; even the elevators must journey a shorter distance.
The trendy model of this system was rediscovered and repackaged by Danish engineer Jorgen Breuning within the late ‘90s, who was impressed by a Danish Ministry of Housing design competitors looking for extra versatile and sustainable buildings. His approach was adopted by a agency that now markets itself as BubbleDeck, which sells across the globe, and makes precast slabs. The Harpa Live performance Corridor in Reykjavík, Iceland, designed by Henning Larsen Architects and accomplished in 2013 using voided concrete, gained the Mies van der Rohe Award.
The approach, which has been utilized in completely different codecs for hundreds of years, is extra in style internationally, with quite a few proprietary techniques angling for market share of the void. Honeycomb-shaped Beeplate, for example, helps you to “construct just like the bees.”
Plechaty has seen such slabs in India and the Center East, and within the U.S., up to date New York-based architect Steven Holl has used it to permit for wider concrete spans that didn’t want further beams for assist. Completely different builders have additionally used extra eclectic supplies to fill the voids: not simply specially-made plastic balls, however styrofoam, and, supposedly, soccer balls.
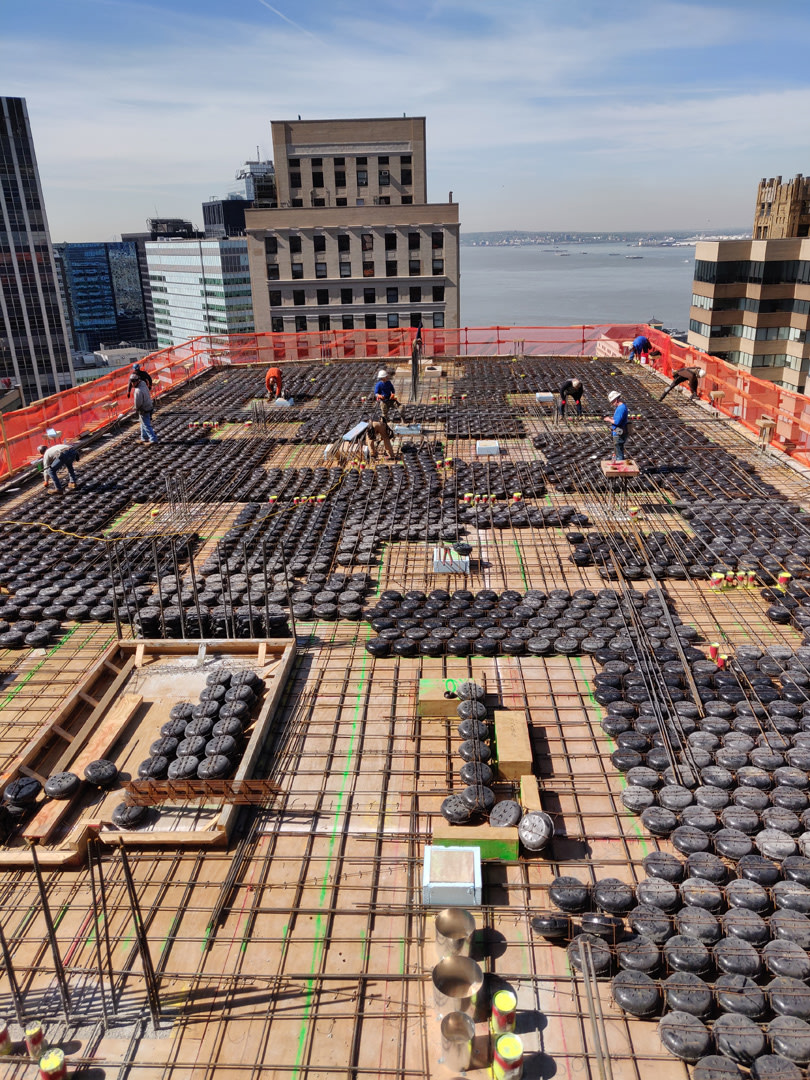
[Photo: courtesy Cobiax]
What Plechaty hasn’t seen is extra trendy buildings in NYC make the most of the approach. It’s not as widespread in New York, he says, as a result of the constructing trades have a tendency to stay to extra conventional strategies. Concrete, comparatively cheap in comparison with different constructing supplies, doesn’t add a lot value to initiatives.
“It’s a wonderful system, and it’s gaining popularity within the final three to 4 years,” says Ramon Gilsanz, an engineer and founding accomplice of Gilsanz Murray Steficek, an engineering and structure agency. “However the trade tends to love to do what they’ve at all times completed.”
However which will change quickly, as a result of renewed consideration on sustainability and simpler availability of voided concrete techniques. The U.S. spinoff of a German firm referred to as Cobiax—CO for the chemical shorthand for carbon dioxide, and BIAX for biaxial, that means two axes—makes proprietary recycled plastic spheres, which have been used on the 1 Wall Road venture. Michael Russillo, CEO of Cobiax USA, says the agency plans to open a manufacturing unit in Massachusetts in mid-2024.
He’s been concerned in this type of development for 11 years, and has bought the agency’s plastic pucks to about 30 completely different initiatives, together with museums and an Amazon warehouse. However he believes they’re on the verge of breaking out.
“Extra individuals must see it,” he says. “Structural engineers, they perceive it pretty simply.”
[ad_2]
Source link