[ad_1]
As an increasing number of People embrace electrical automobiles, automakers and the federal authorities are racing to safe the supplies wanted to construct EV batteries, together with by pouring billions of {dollars} into battery recycling. Right this moment, recyclers are targeted on recovering worthwhile metals like nickel and cobalt from spent lithium-ion batteries. However with the commerce warfare between the U.S. and China escalating, some at the moment are taking a better have a look at one other battery mineral that right now’s recycling processes deal with as little greater than waste.
On December 1, China applied new export controls on graphite, the carbon-based mineral that’s greatest recognized for being utilized in pencils however that’s additionally utilized in a extra refined type in industrial EV battery anodes. The brand new insurance policies, which the Chinese language authorities announced in October shortly after the Biden administration increased restrictions on exports of superior semiconductors to China, have alarmed U.S. lawmakers and raised concerns that battery makers outdoors of China will face new challenges securing the supplies wanted for anodes. Right this moment, China dominates every step of the battery anode supply chain, from graphite mining and artificial graphite manufacturing to anode manufacturing.
Together with a brand new federal tax credit score that rewards automakers that use minerals produced in America, China’s export controls are boosting the U.S. auto business’s curiosity in domestically sourced graphite. However whereas it may take a few years to arrange new graphite mines and manufacturing services, there’s one other, doubtlessly quicker choice: Harvesting graphite from useless batteries. As U.S. battery recyclers construct large new services to get better expensive battery metals, some are additionally making an attempt to determine how one can recycle battery-grade graphite — one thing that isn’t carried out at scale wherever on this planet right now resulting from technical and financial limitations. These firms are being aided by the U.S. Division of Vitality, which is now pouring tens of hundreds of thousands of {dollars} into graphite recycling initiatives geared toward answering primary analysis questions and launching demonstration vegetation.
If the challenges holding again industrial graphite recycling will be overcome, “the used graphite stream could possibly be enormous,” Matt Keyser, who manages the electrochemical power storage group on the the Division of Vitality’s Nationwide Renewable Vitality Laboratory, advised Grist. Along with boosting home provides, recycling graphite would forestall crucial battery assets from being wasted and will cut back the carbon emissions tied to battery manufacturing.
To know why graphite is difficult to recycle, a bit of fabric science is important. Graphite is a mineral type of carbon that has each metallic and non-metallic properties, together with excessive electrical and thermal conductivity and chemical inertness. These qualities make it helpful for a wide range of power and industrial functions, together with storing power inside lithium-ion batteries. Whereas a lithium-ion battery is charging, lithium ions move from the metallic cathode into the graphite anode, embedding themselves between crystalline layers of the carbon atoms. These ions are launched whereas the battery is in use, producing {an electrical} present.
Recycled graphite connected to air bubbles at a graphite recycling laboratory in Freiberg, Germany. [Photo: Jens Schlueter/AFP/Getty Images]
Graphite will be present in nature as crystalline flakes or lots, that are mined after which processed to supply the small, spherical particles wanted for anode manufacturing. Graphite can be produced synthetically by heating byproducts of coal or petroleum manufacturing to temperatures larger than 2,500 levels Celsius (about 4,500 levels Fahrenheit) — an energy-intensive (and sometimes emissions-intensive) course of that triggers “graphitization” of the carbon atoms.
Comparatively low cost to mine or manufacture, graphite is decrease in worth than lots of the metals inside battery cathodes, which might embrace lithium, nickel, cobalt, and manganese. Due to this, battery recyclers historically haven’t taken a lot curiosity in it. As a substitute, with many battery recyclers hailing from the metals-refining enterprise, they’ve targeted on what they already knew how one can do: extracting and purifying these cathode metals, typically of their elemental type. Graphite, which might comprise as much as 30% of an EV battery by weight, is handled as a byproduct, with recyclers both burning it for power or separating it out to be landfilled.
“Up till lately, individuals speaking about recycling for batteries actually went after these token [metal] components as a result of they have been excessive worth . . . and since that recycling course of can overlap fairly a bit with standard steel processing,” Ryan Melsert, the CEO of U.S. battery supplies startup American Battery Expertise Firm, advised Grist.
For graphite recycling to be worthwhile, recyclers must acquire a high-performance, battery-grade product. To take action, they want strategies that separate the graphite from all the pieces else, take away any contaminants like metals and glues, and restore the fabric’s authentic geometric construction, one thing that’s typically carried out by making use of intense heat.
Crude recycling approaches like pyrometallurgy, a standard course of during which batteries are smelted in a furnace, received’t work for graphite. “Greater than doubtless you’re going to burn off the graphite” utilizing pyrometallurgy, Keyser mentioned.
Right this moment, the battery recycling business is shifting away from pyrometallurgy and embracing hydrometallurgical approaches, during which useless batteries are shredded and dissolved in chemical options to extract and purify numerous metals. Chemical extraction approaches could possibly be tailored for graphite purification, though there are nonetheless “logistical points,” based on Keyser. Most hydrometallurgical recycling processes use robust acids to extract cathode metals, however these acids can harm the crystalline construction of graphite. An extended or extra intensive warmth remedy step could also be wanted to revive graphite’s form after extraction, driving up power utilization and prices.
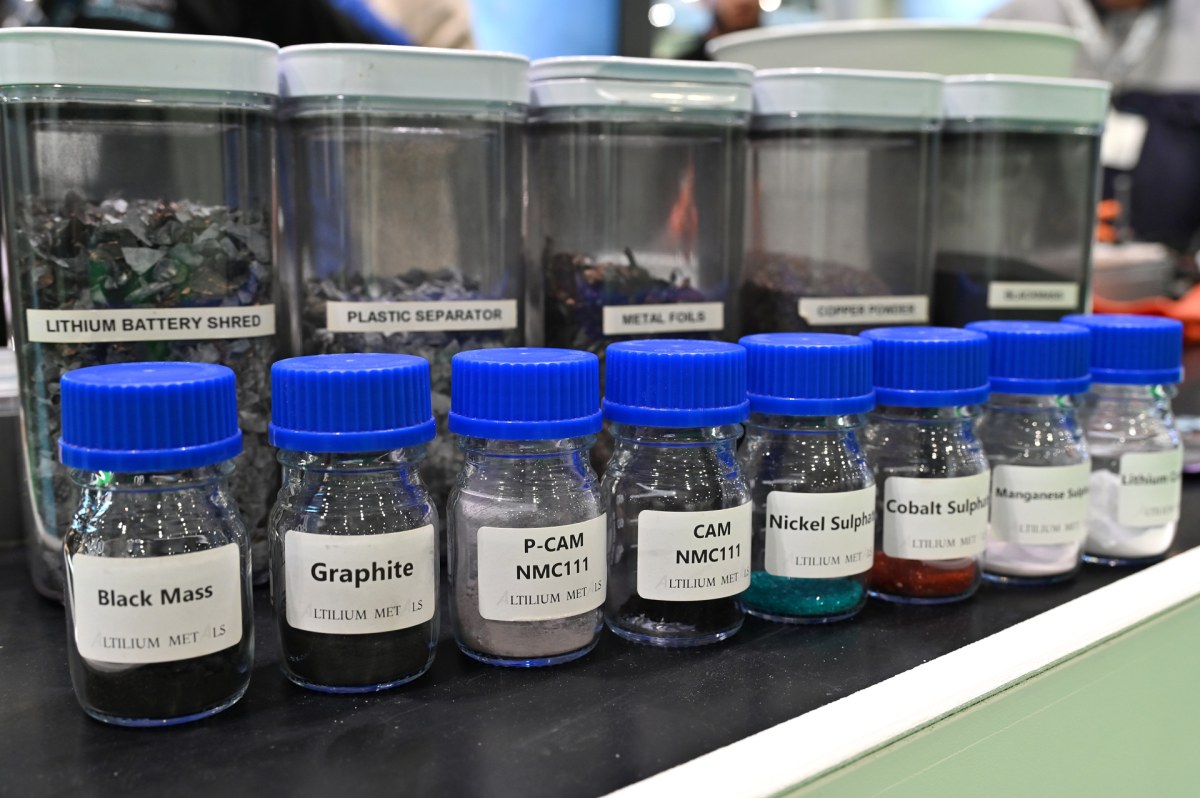
Parts and different supplies reclaimed from electrical car batteries, together with graphite, are displayed throughout the London EV Present in November 2023. [Photo: John Keeble/Getty Images]
A 3rd method is direct recycling, during which battery supplies are separated and repaired for reuse with none smelting or acid remedy. This gentler course of goals to maintain the construction of the supplies intact. Direct recycling is a more recent concept that’s farther from commercialization than the opposite two strategies, and there are some challenges scaling it up as a result of it depends on separating supplies very cleanly and effectively. However recent research suggests that for cathode metals, it may well have vital environmental and value advantages. Direct recycling of graphite, Keyser mentioned, has the potential to make use of “far much less power” than artificial graphite manufacturing.
Right this moment, firms are exploring a spread of graphite recycling processes.
American Battery Expertise Firm has developed an method that begins with bodily separating graphite from different battery supplies like cathode metals, adopted by a chemical purification step. Extra mechanical and thermal remedies are then used to revive graphite’s authentic construction. The corporate is at the moment recycling graphite at a “very small scale” at its laboratory services in Reno, Nevada, Melsert mentioned. However sooner or later, it plans to scale as much as recycling a number of tons of graphite-rich materials a day with the assistance of a three-year, almost $10 million Department of Energy grant funded by means of the 2021 bipartisan infrastructure regulation.
Massachusetts-based battery recycling startup Ascend Parts has additionally developed a chemical course of for graphite purification. Dubbed “hydro-to-anode,” Ascend Parts’ course of “comes from among the work we’ve carried out on hydro-to-cathode,” the corporate’s patented hydrometallurgical process for recycling cathode supplies, mentioned Roger Lin, the vice chairman of world advertising and authorities relations on the agency. Lin mentioned that Ascend Parts is ready to take graphite that’s been contaminated throughout an preliminary shredding step again to 99.9% purity, exceeding EV business necessities, whereas additionally retaining the fabric properties wanted for prime efficiency anodes. In October, Ascend Parts and Koura World announced plans to construct the primary “superior graphite recycling facility” within the U.S.
The Division of Vitality-backed startup Princeton NuEnergy, in the meantime, is exploring direct recycling of graphite. Final 12 months, Princeton NuEnergy opened the first pilot-scale direct recycling plant within the U.S. in McKinney, Texas. There, batteries are shredded and a collection of bodily separation processes are used to kind out completely different supplies, together with cathode and anode supplies. Cathode supplies are then positioned in low-temperature reactors to strip away contaminants, adopted by further steps to reconstitute their authentic construction. The identical normal method can be utilized to deal with anode supplies, based on founder and CEO Chao Yan.
“From day one, we’re pondering to get cathode and anode materials each recycled,” Yan mentioned. However till now, the corporate has targeted on commercializing direct recycling for cathodes. The rationale, Yan mentioned, is straightforward: “No buyer cared about anode supplies prior to now.”
That, nonetheless, is starting to alter. Yan mentioned that over the previous 12 months — and particularly in the previous few months since China introduced its new export controls — automakers and battery producers have taken a larger curiosity in graphite recycling. Melsert additionally mentioned that he’s beginning to see “very vital curiosity” in recycled graphite.
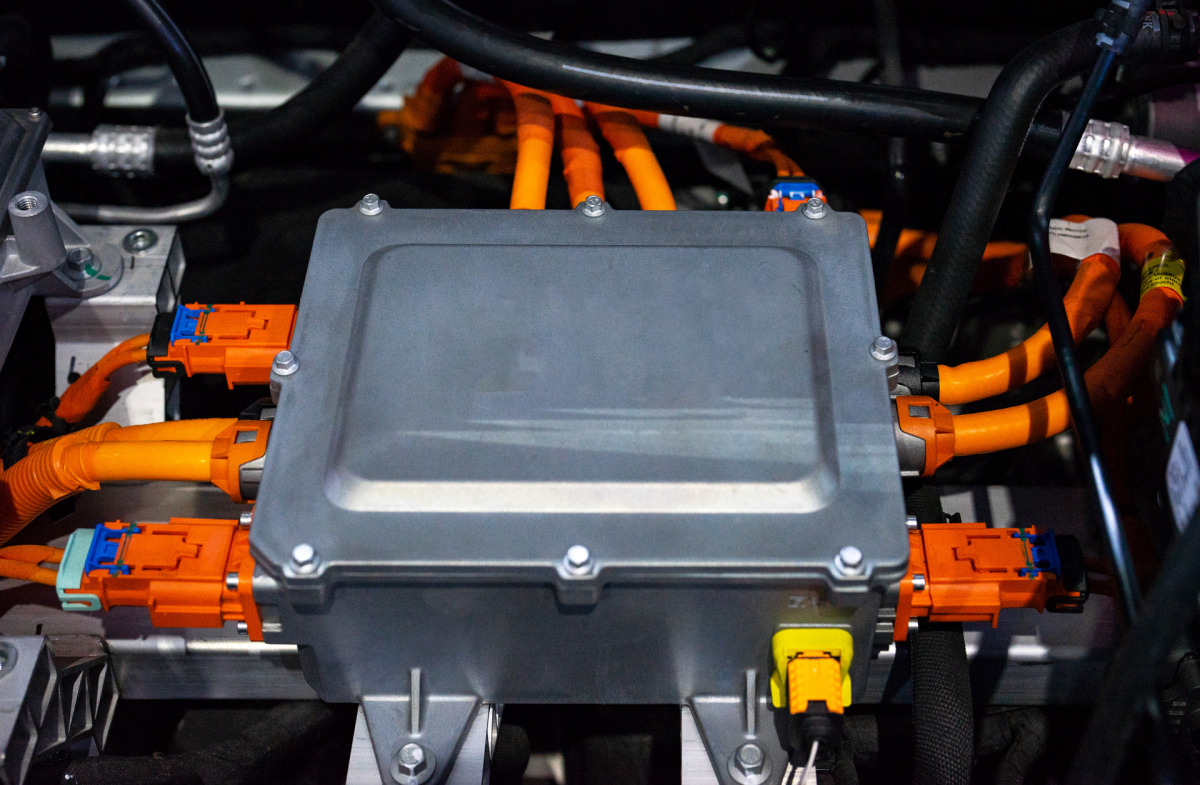
A lithium-ion battery pack and wiring connections inside an electrical car. [Photo: Prapass Pulsub/Getty Images]
Nonetheless, clients must wait a little bit longer earlier than they will buy recycled graphite for his or her batteries. The strategies for purifying and repairing graphite nonetheless want refinement to scale back the price of recycling, based on Brian Cunningham, the batteries R&D program supervisor on the Division of Vitality’s Car Applied sciences Workplace. One other limiting step is what Cunningham calls the “supplies qualification step.”
“We have to get recycled graphite to a degree the place firms can present materials samples to battery firms to judge the fabric,” Cunninghamsaid. The method of shifting from very small-scale manufacturing to ranges that enable EV makers to check a product, “may take a number of years to finish,” he added. “As soon as the recycled graphite enters the analysis course of, we must always begin to see an uptick in firms establishing pilot- and commercial-scale tools.“
Provide chain considerations may speed up graphite recycling’s journey to commercialization. Over the summer time, the Division of Vitality added pure graphite to its list of critical materials for power. Graphite can be on the U.S. Geological Survey’s list of critical minerals — minerals which might be obligatory for superior applied sciences however vulnerable to provide disruptions.
This classification signifies that domestically sourced graphite can assist EVs qualify for the “clear car credit score,” a tax credit score that features strict requirements round crucial mineral sourcing following the 2022 Inflation Discount Act. To qualify for the total credit score, EV makers should acquire a big fraction of their battery minerals from the U.S. or a free-trade associate. By 2025, their automobiles could not include any crucial minerals extracted or processed by a “international entity of concern” — an entity related to a shortlist of international nations that includes China. This requirement may “drive a premium” for domestically recycled graphite, Lin mentioned.
Tax incentives could possibly be key to serving to recycled graphite compete with virgin graphite, based on Yuan Gu, a graphite analyst on the consulting agency Benchmark Mineral Intelligence. Regardless of China’s new export controls, Gu expects graphite to stay comparatively low cost within the close to future resulting from an “oversupply” of graphite available on the market proper now. Whereas Gu mentioned that graphite recycling is “positively on radar for Western nations” excited by securing future provides, its viability will rely upon “how expensive or low cost the recycled materials might be.”
If graphite recycling does catch on, business insiders are hopeful will probably be in a position to meet a big fraction of the nation’s future graphite wants — that are growing rapidly because the clear power transition accelerates — whereas making the whole EV battery provide chain extra sustainable.
“You may assist regional provide chains, you may assist with effectivity, with carbon footprints,” Lin mentioned. “I believe it’s a no brainer this can occur.”
[ad_2]
Source link